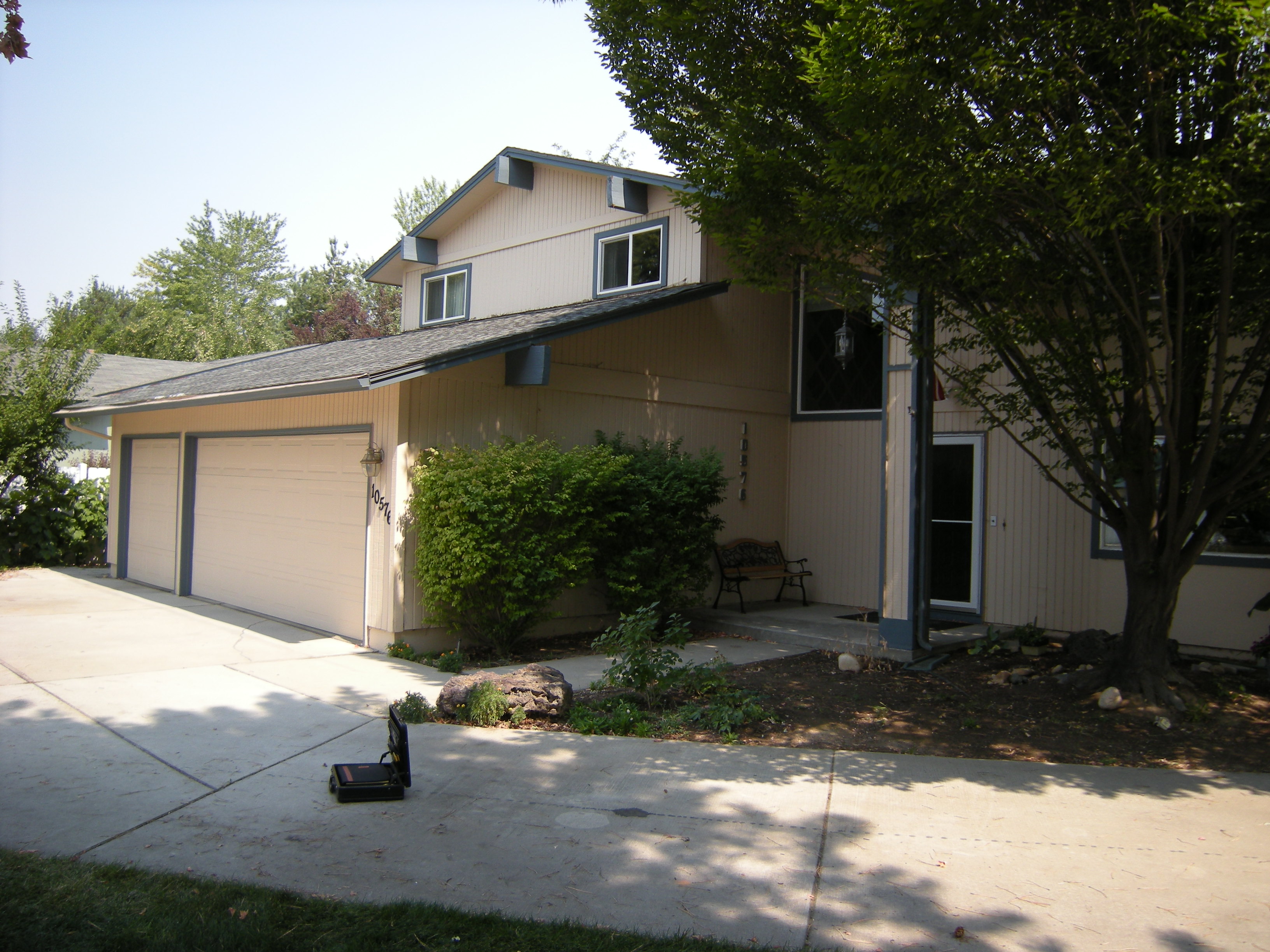
Before
We recently completed an addition with a twist. Many have done drive by’s of our project on Five Mile Road. Few have commented on our amazing structural engineering feat.
This is rare and not something that happens every day. Granted it looks pretty normal to the casual observer but there is some magic involved when structures are hanging over their supporting walls in two different direction without the use of pillars to support them.
What started as a simple garage overbuild turned into an amazing solution to a complicated problem, almost on the fly.
One overhang, no problem
The plan that was provided by the homeowner included a deck with the typical posts to support it, I was not comfortable with the plan and was bound and determined not to need the posts. (Primarily because they get bumped into) We simply eliminated the posts from the plans using a common cantilevered floor joist system approach.
Once underway the client decided he wanted to overbuild the garage entrance up to the maximum allowable setback. This would add another 4 feet beyond the front of the existing garage. With so much of the new structure overhanging in two different directions, I was afraid we would be required to use support posts but determined to explore all of our options. This is when the Change Order process kicked in.
Two overhangs in opposite directions, now that gets complicated
Determined to find a solution, I called a meeting on the job site between our trusty structural engineer Scott Soule, our veteran project manager Steve Wadsworth, and myself, to see what could be done.
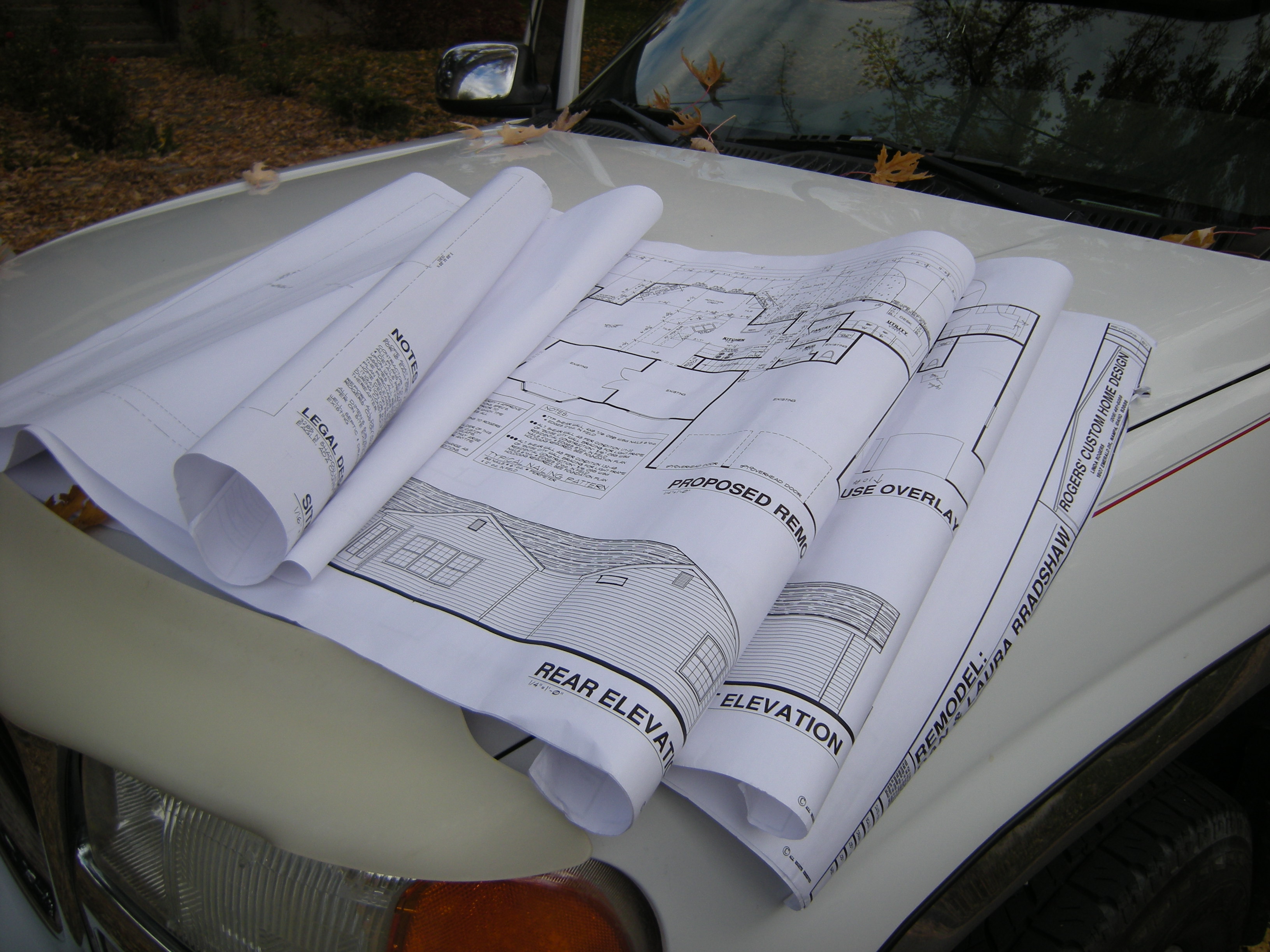
The plans
Cantilevering in two directions would be difficult because of the requirements for cantilevers which state that 2/3’s of the cantilevered component much be within the structure.
I was not going to add an ugly support post without a fight. After scratching our heads and talking the site we laid out the plans on the hood of Scott’s truck, started sketching, and tossing around some idea.
After about 15 minutes of “What ifs” and “Hey I knows” We discovered is if we change the layout of the floor joists and add a rim beam, that we could do a double cantilever and viola problem solved in theory. With high fives all around we split up and went on about our business with the confidence of a high performance team. Scott retired to his office to do the necessary calculations and confirm that we could make it happen.
The proof is in the puddin’, Ta-Da
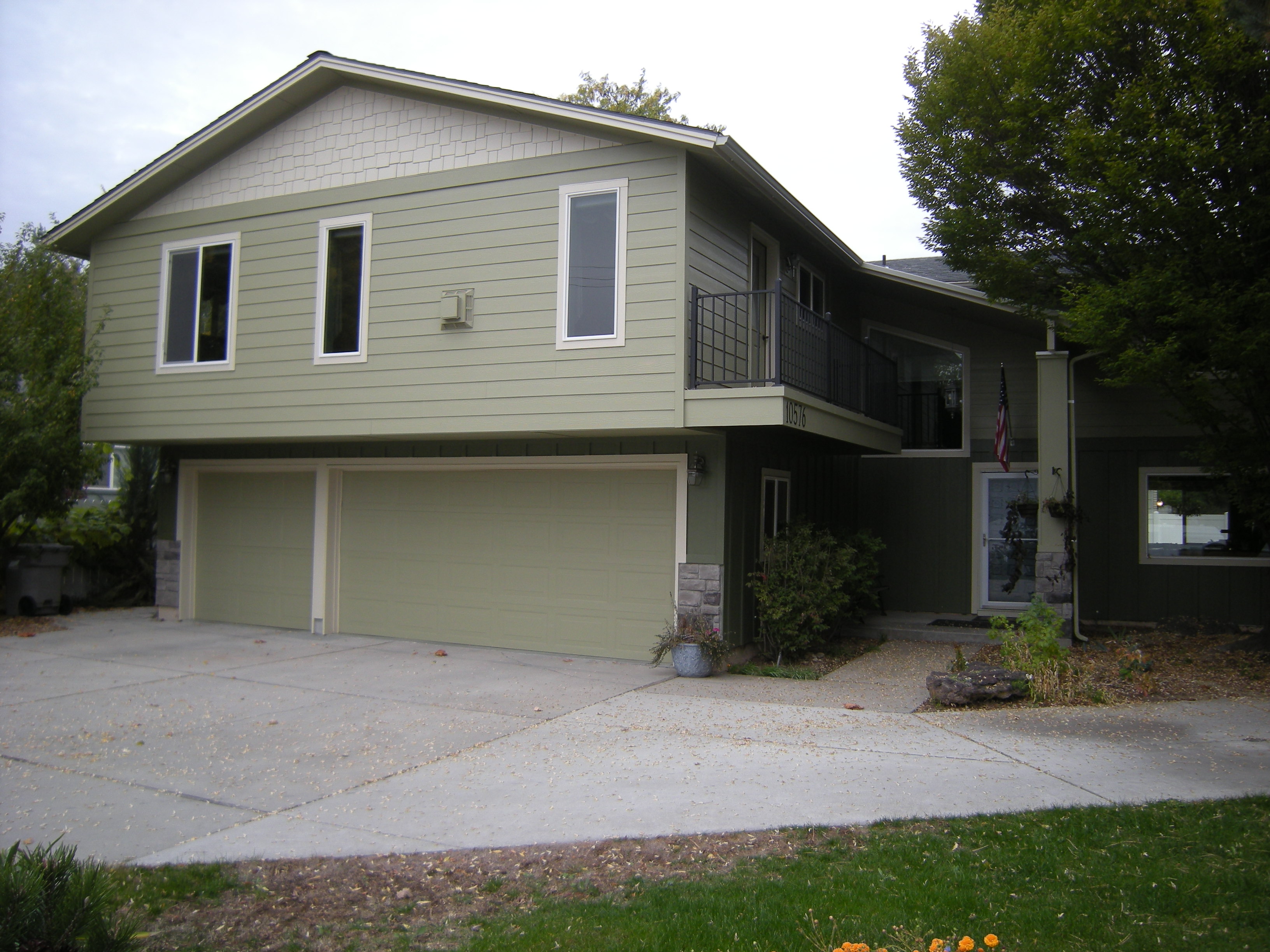
No visible Means of Support!
Solving these problems does not happen in a vacuum, it takes experience, talent and a genuine desire to work in a collaborative way.
The best part was when the framing inspector came by to sign off on the project. “That is amazing, he said…How did you do that? It looks great, oh I see how it works now, I’m not sure I have ever seen this technique used.” Music to our ears.
This is where the gooey stuff is in remodeling for us all. We are driven to solve problems and create solutions to complicated remodeling problems with a team approach that cannot be beat.
Your comments are welcome. To ask questions or get more information about remodeling, click here to email me directly, or call 208-947-7261
If you or someone you know is considering remodeling or just wants to speak to a trustworthy remodeling contractor please contact me, you’ll be glad you did.
what was the layout of the joists that allowed this solution? I would like to have a double cantilever on an outbuilding but don’t know how to approach it without posts(way better without). thanks for your ingenuity and help.
What happened is that the primary lay over the garage was parallel with the garage door then we changed it so that 1/3 would hang over the front of the structure and 1/3 hung over the right side (as you were looking at the garage) Then we used a large beam across the front attached to the tails and that tied to the tails of the rafters cantilevered over the tight side and everything was suspended without posts. I could send you a sketch or be happy to discuss it further. The cantilever rule is that 2/3 of board must be inside the building.
Hi Joe, I am trying to solve a similar problem, in my case an elevated attached deck that I would like to have cantilevered on two adjacent sides. If you could provide any additional details or a sketch, it would be greatly appreciated. Thanks,
Chris
Chris I have done a sketch and will send it directly the key is to have 2/3 of the cantilevered beam inside the structure. By changing the direction of the floor joists we were able to do this with ease. It is a bit of a puzzle, once you figure it out you wont forget. Joe
Joe, any chance I could see the sketch as well? Am trying to minimize foundation footprint and maximize sf for new build. Thanks!
Waylon, I will send you what you need shortly. Thanks for asking. Hope it helps. Joe